
Anode Sheets
All anode sheets from lead and lead alloys are produced according to a rolling procedure developed at JL Goslar. Many advantages result compared with conventionally cast anodes which make the electrolysis process more efficient and cost effective:
• higher density
• lower porosity
• defined grain structure
• lower creep tendency
• higher conductivity
• higher resistance to passivation
• lower oxygen overpotential
This means a rolled anode has optimum corrosion resistance, deformation stability and energy efficiency. The long lifetime of the anode leads to higher productivity and lower operating costs.
We can also treat the anode plates in the ABG procedure on request. Through the rapid development of the necessary PbO2 and MnO2 layers the anode reaches its full capacity within a short period of time and helps the electrolysis operator to operate their plant at the highest level of production.
JL Goslar is in the position of being able to produce all the required anode plate dimensions: small-sized anodes (up to 2 m2), jumbo anodes (up to 3 m2) or even mega-jumbo anodes (more then 3 m2). Up to today, the biggest JL anode had a total area of 3,8 m2. The plate thickness is on average 8 to 11 millimeter in the zinc extraction and 6 to 15 millimeter in the copper extraction.
The product range is supplemented with plate sections to improve the flow rate or to increase the current density and for the attachment of spacers.
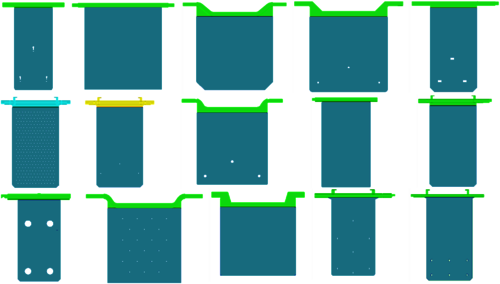